
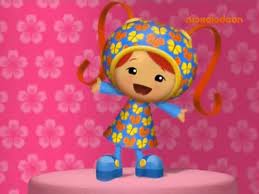
The use of these materials renders microscale machines that undergo complex stimuli‐responsive transformation such as from planar to 3D by combining spatial design like introducing in‐plane or out‐plane differences. Structures fabricated by these materials undergo mechanical motion under stimulation such as temperature, pH, light, and so on. To achieve this goal, shape‐morphing smart polymers like hydrogels, liquid crystalline polymers, and other smart polymers are of great interest. In particular, microscale polymer machines that can perform intelligent work for manipulation or transport, adaptive locomotion, or sensing are in‐demand. Microscale machines are able to perform a number of tasks like micromanipulation, drug‐delivery, and noninvasive surgery. The results obtained from the simulation and experiments provide information for deciding the optimum parameters for printing chitosan-based ink with high quality. The effect of different printing settings was studied during the experimental test. Moreover, the model validation of the printed chitosan hydrogel was investigated to confirm the simulation outcomes for high-quality printing. Furthermore, the impact of different velocities and viscosities in extrusion-based chitosan 3D printing was investigated. The flow was presumed to be laminar and two-phased in the simulations. This study employed multiphysics simulation to predicate the potential printability of chitosan hydrogel as a desirable biomaterial used in tissue engineering.
#Milli power of ten trial#
However, it typically uses trial and error techniques to achieve a three-dimensional structure, which wastes material and time.
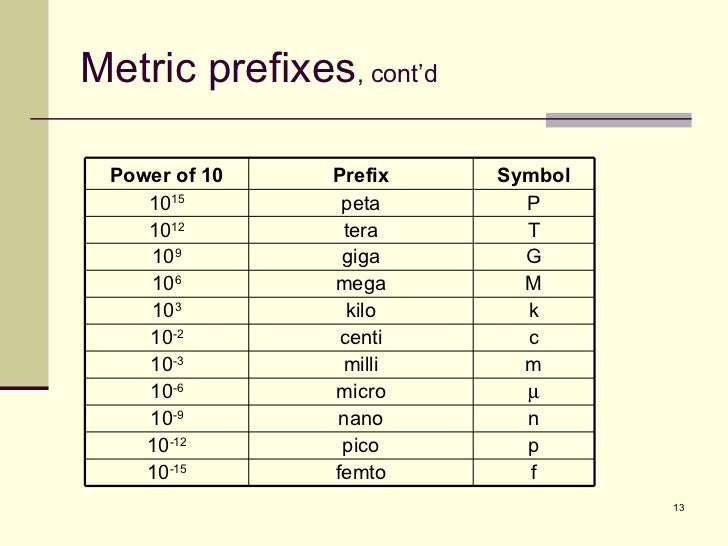
The 3D printing hydrogel-based ink requires crucial properties, such as printability and printing fidelity to fabricate the appropriate structure. Extrusion-based three-dimensional (3D) printing has recently become a major field that provides significant benefits, as it is principally employed to fabricate 3D scaffolds, exploiting soft biomaterials.
